Environmental Management System (EMS)
Our environmental management policy declares an active commitment to address environmental challenges facing society, including not only preventing environmental pollution but also building circular economies, delivering carbon neutrality, reducing environmental impacts, protecting water resources and conserving biodiversity as key management challenges. Under this policy we are striving to improve our environmental performance.
Environmental Management Policy
In January 2006 we formulated our Environmental Management Policy, reflecting the fact that we consider an active commitment to the environmental challenges facing society to be key management challenges. We will focus on the following six items in all business operations, whilst also communicating with a wide range of stakeholders, both internationally and locally. As a member of the GCCA and the UNGC, we will pursue a sustainable cement industry.
Formulated in January 2006
Revised in April 2024
- Pursuing Environmentally Conscious Business Activities
We will properly evaluate the environmental impact of our business activities and work to reduce the burden on the environment by developing and adopting ecoconscious products and technologies. As a member of the local community, we will also engage in environmental conservation activities. - Compliance with Environmental Laws and Regulations
We will ensure compliance with all environmental laws and regulations applicable to our business activities. - Contribution to the creation of Circular Economies
We will contribute to the establishment of circular economies to reduce our environmental impact and promote economic growth by utilizing the characteristics of the cement industry and advancing the sophistication of recycled resource utilization technologies. - Initiatives to deliver Carbon Neutrality
We will work to achieve carbon neutrality throughout the supply chain as a company by maximizing the use of existing technologies and developing and sequentially deploying innovative technologies. - Promoting Global Technology Transfer
We will promote the worldwide transfer and deployment of our energy conservation, environmental preservation and waste utilization technologies. - Nature Conservation
By providing products and technologies that respect coexistence with nature, we will contribute to the conservation and restoration of water resources and biodiversity, and aim to achieve a nature-positive society.
We have established an Environmental Management Committee chaired by the officer in charge of the Production Department to promote environmental management and implement the Environmental Management System (EMS).
In June 1997 we initiated ISO 14001 certification of each of our plants and attained certification of all six of our directly operated plants by 1999. In 2009, we established a companywide Environmental Management System (EMS) that extends to our headquarters, branches, and the Central Research Laboratory, and in February 2024, we underwent our fifth renewal audit as a company by the Japan Testing Center for Construction Materials, and continue to maintain our certification.
In countries where ISO is adopted, the ISO 14001 certification acquisition rate for cement plants, including Group companies, is 100% and are actively committed to environmental conservation. Furthermore, all of our overseas cement plants where ISO is not adopted as the mainstream standard operate their own EMS.
Risk Management
- Environmental risk reduction
We are taking necessary measures to prevent major environmental accidents as appropriate based on past cases. - Response to natural disasters
In recent years, the intensification of natural disasters due to abnormal weather has become a challenge. We plan to identify the risk of flooding in our plants due to heavy rain, confirm drainage routes and treatment capacity, and then invest in any necessary preventative measures. - Compliance with environmental laws
To ensure compliance with environmental laws throughout the Taiheiyo Cement Group, we regularly conduct environmental patrols at our group companies to confirm their compliance status.
We will implement continuous improvement activities through the reliable operation of our EMS, and will steadily work on the following points:
- Zero serious environmental accidents and complaints
We provide training using past cases of serious environmental accidents. To eliminate environmental accidents and complaints caused by dust emissions, we will completely transition the cement kiln exhaust gas treatment equipment from electrostatic precipitators to bag filters at six directly managed plants and three group company plants. - Creating plants that are resilient to emergencies (earthquakes, tsunamis, oil spills, torrential rains, fires, dust emissions)
By reviewing manuals for each emergency situation and conducting regular education and training, we will develop human resources with the on-site capabilities to respond to any emergency. We aim to create plants that are resilient to emergencies by identifying environmental risks and planning and implementing countermeasures. - Establishing a system for compliance with environmental laws throughout the Group
For group companies, we will conduct regular environmental patrols using checklists that reflect revisions to environmental laws, and establish a system to maintain compliance with environmental laws and regulations.
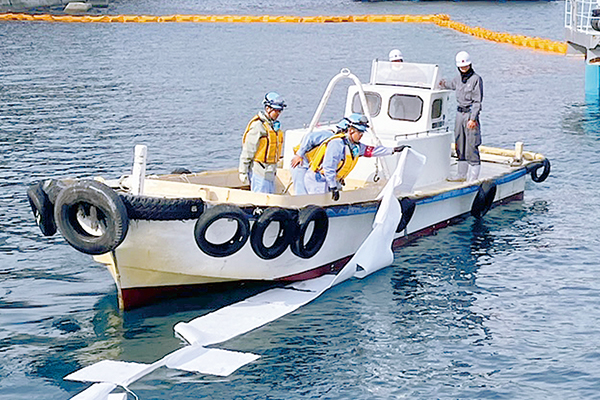
Training to respond to environmental accidents (Oita Plant)
Internal Environmental Audits
We conducted internal environmental audits at all our sites in FY2024. This year's audit focused on confirming compliance evaluations for environmental laws and other requirements, reviewing external communications, and verifying corrective actions for unmet targets. For plants, it also included following up on corrective and preventive actions for environmental non-conformities and assessing flood risk to equipment from natural disasters, including the formulation of countermeasures; and for branches, it involved verifying emergency response procedures at service stations.
Total number of identified issues | Number of requests for improvement | Number of corrective actions taken | |
FY2022 | 40 | 3 | 3 |
FY2023 | 29 | 3 | 3 |
FY2024 | 26 | 5 | 5 |
Reducing Environmental Impact
Based on our environmental management policy, we comply with environmental laws and regulations and engage in business activities that consider the environment.
Each plant maintains emergency response plans in preparation for possible environmental accidents. They also conduct periodic fire-fighting drills in cooperation with local fire departments. Other training includes how to reduce environmental impact when an environmental accident occurs, and how to report it to local authorities.
In addition, as we increasingly utilize ever more diverse forms of waste and by-products, the number of environmental issues we need to consider also increases. Therefore, we are ramping up our efforts to reduce environmental impact through activities such as expanding indoor storage facilities and the use of sealed containers for waste and by-products, and improving our flue gas stacks. On receiving an environmental complaint, whenever possible we quickly travel to the site in question to check the situation, investigate the cause and provide an explanation. If we find that our activities are the cause we implement improvements.
Water Contamination Prevention
Most of the industrial water discharged from our plants to public watercourses is cooling water and not polluted as defined in the Water Pollution Control Act. At our cement plants all water resources are reused as circulation water to minimize industrial water discharge into watercourses. Moreover, we are taking measures to prevent the leakage of contaminants by installing bunds around oil tanks and acid/alkali tanks, as well as installing sedimentation tanks, water-oil separation tanks, oil film detectors, pH meters and suspended solid sensors on water discharge routes that connect to publiccourses.
Air Pollution
Air pollutants generated from cement production are primarily NOx, SOx and dust in combustion gases emitted from cement kilns. To ensure the proper management of these substances we strive to reduce air pollutant emissions through measures such as installing equipment to continuously monitor emission concentrations, improving NOx reduction systems and installing bag filter equipment to capture dust. Our target is to maintain our FY2011 emissions levels.
Soil Contamination Prevention
Across FY2008 and FY2009, we evaluated the risks associated with cement plants that may be sited on contaminated ground by appointing an expert consultant to undertake a land history survey, conduct drilling surveys, and verify whether or not the soil is contaminated. Actions have been taken as necessary based on the findings, such as the installation of observation wells to monitor ground water contamination and the removal of contaminated soil. We are also working to eliminate the possibility of soil contamination via measures to prevent the leakage of wastewater from scrapyards or fluid from oil tanks, acid/alkali tanks, pipes and so forth.
Management of PCB Waste
We properly store and dispose of high and low concentrations of PCB waste in accordance with the Amendment to the Law concerning Special Measures for Promotion of Proper Treatment of PCB Wastes (hereinafter referred to as the PCB Special Measures Law).
For high-concentration PCB waste with an early disposal deadline as stipulated by the PCB Special Measures Law, we signed a processing contract with the Japan Environmental Safety Corporation (JESCO) in 2006 and have prioritized processing.
In FY2024, we disposed of six PCB contaminated items, such as electrical ballasts, from the former Osaka Plant and the former Kawara Plant, completing the disposal of all high-concentration PCB waste. However, two contaminated items were subsequently discovered at the Kumagaya Plant and the former Onoda Plant and are currently being stored. We will respond appropriately in accordance with instructions from local authorities.
(No. of items)
Waste | Treated in FY2023 | New Targets for FY2024 | FY2024 processing results | Stored in FY2024 | Treatment Scheduled for FY2025 |
Capacitors | 0 | 0 | 0 | 0 | 0 |
Transformers | 0 | 0 | 0 | 0 | 0 |
Electrical ballasts | 6 | 2 | 6 | 2 | 2 |
Total | 6 | 2 | 6 | 2 | 2 |
Foundation insulation system "Sotodan"
The housing industry is promoting the spread of ZEH*, with excellent environmental performance, towards the delivery of carbon neutrality by 2050. ZEH requires high thermal insulation performance to reduce energy consumption. One way to improve thermal insulation performance is the foundation insulation method, which covers the concrete foundation with insulation material. This makes it possible to keep the underfloor temperature constant, making it cool in summer and warm in winter. Furthermore, by combining this with roof and wall insulation, energy consumption for air conditioning and floor heating can be significantly reduced. "Sotodan," developed by Chichibu Concrete Industry Co., Ltd. for foundation insulation, is a construction method that protects the insulation material on the outside of the foundation from impact, wind, rain, and ultraviolet rays, and adds design value. It is a simple construction method that allows various materials to be applied over the insulation material without any special skills or tools, and it has excellent adhesion and durability.
As compliance with energy-saving standards will be mandatory for all new buildings from April 2025, ZEH is expected to increase further in the future, and demand for "Sotodan" is also expected to increase accordingly.
* ZEH: Abbreviation for net Zero Energy House, meaning "a house with zero or negative energy balance" consisting of three elements: energy saving, high thermal insulation and energy generation, contributing to CO2 reduction.
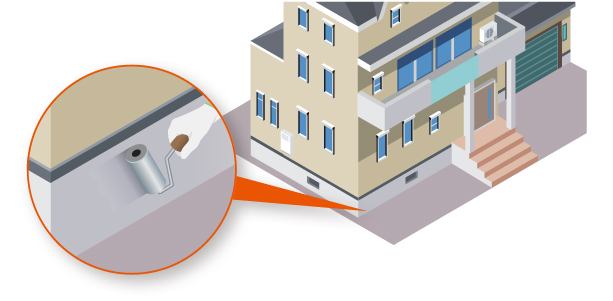
"Sotodan" is a method of applying various materials over the insulation material covering the concrete foundation of a house
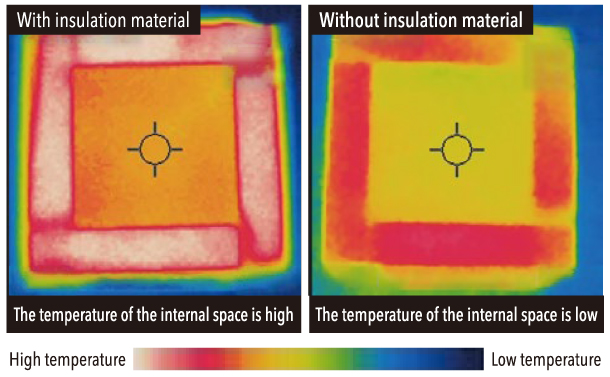
When placed in a low-temperature environment for 3 hours, the temperature of the internal space of the concrete test specimen is kept high under the condition with insulation material installed (left figure)