In response to social needs for environmental conservation, we leverage the advantages of the cement and related technologies we have cultivated over the years to provide environmentally sound products and services that contribute to resource conservation and CO2 reduction.
Low-CO2 emission limestone-blended cement "ADVANCEMENT"
Our U.S. group company, CalPortland Company, has launched a new product series called ADVANCEMENT, which is a blend of Portland cement and limestone. By replacing up to 15% of clinker with limestone ADVANCEMENT is a low-CO2 emission product that can reduce CO2 emissions by approximately 10% compared to ordinary Portland cement as specified by ASTM C150.
ADVANCEMENT TYPE 1L complies with ASTM C595 and AASHTO M240 and is also certified by the California Department of Transportation, allowing it to be widely used in infrastructure construction, including highways. Following test marketing in 2021, CalPortland Company will gradually switch from ordinary Portland cement (TYPE II/V) produced at its Mojave Plant to ADVANCEMENT TYPE 1L. Approximately 1.2 million tonnes of ADVANCEMENT will be produced annually, reducing CO2 emissions by approximately 95,000 tonnes. ADVANCEMENT LT is light-colored and aesthetically pleasing while maintaining the low-CO2 emission performance, and can be used in applications to meet the aesthetic expression of architects and designers. In addition, ADVANCEMENT HS is suitable when particularly high sulfate resistance is required. In this way, ADVANCEMENT is a series of low-CO2 emission cement products that are tailored to the application and performance requirements.
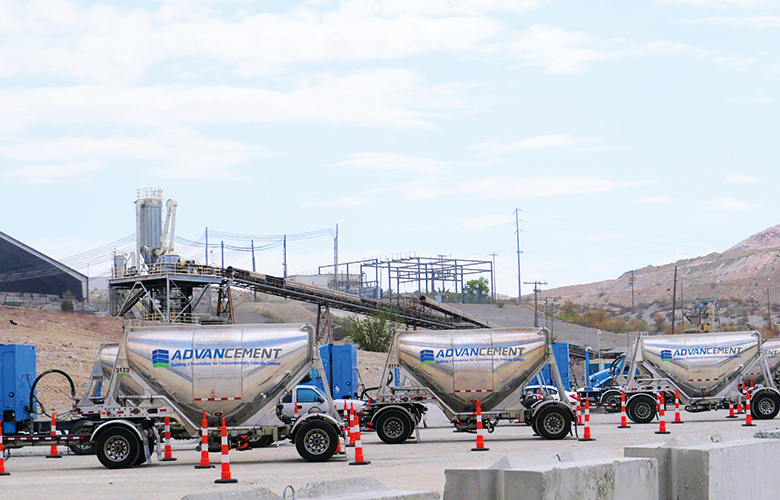
ADVANCEMENT delivery trucks
Thermal Insulating Paving Blocks "Thermalbarrier ILB”
At Taiheiyo Precast Concrete Industry, we sell "Thermalbarrier ILB," which are paving blocks that suppress the absorption of heat from solar radiation, thereby reducing the rise in temperature and heat retained in the road surface, and mitigating the hot environment in pedestrian and roadside areas. The surface layer of this block is made of material that is highly effective in reflecting near-infrared radiation, and the base layer is made of concrete with cavities to reduce the absorption and retention of heat from solar radiation. This contributes to limiting the heat island effect by reducing not only the daytime hot environment but also heat radiation at night.
The performance of the Thermalbarrier ILB was confirmed to be effective in reducing road surface temperature by 11.5°C or more in a comparison test with asphalt pavement conducted by the Japan Interlocking Block Pavement Engineering Association, and has been certified as "COOL BLOCK PAVE". In addition to its excellent thermal insulation performance, the Thermalbarrier ILB series also includes a product that, depending on the specifications of the base concrete layer, provides the block itself with water retention performance and permeability to allow rainwater to permeate into the roadbed. This product also effectively uses crushed roof tiles, molten slag produced in the cooling process after incineration of municipal waste, and glass cullet made from processed wine bottles, which would normally be disposed of as industrial waste, as recycled aggregates.
Recently, Thermalbarrier ILB has been widely used in construction projects, such as Oi Central Seaside Park Sports Forest and Kumagaya Sports Culture Park in Saitama Prefecture.
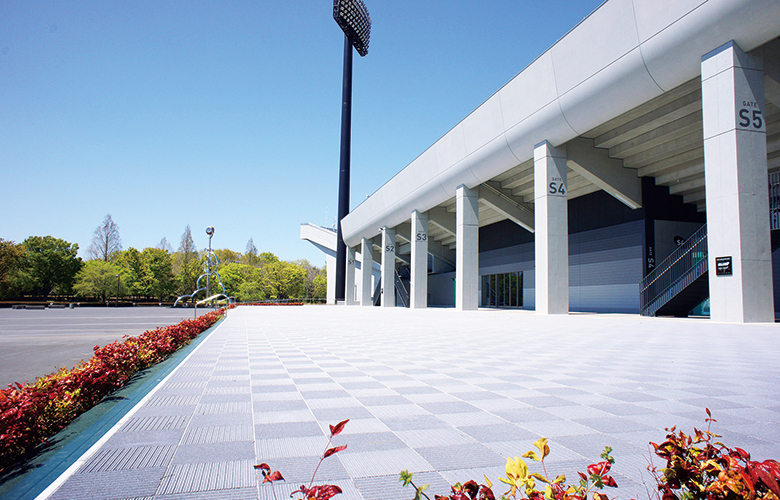
Construction example: Thermalbarrier ILB laid around the rugby field at Kumagaya Sports Culture Park, Saitama Prefecture