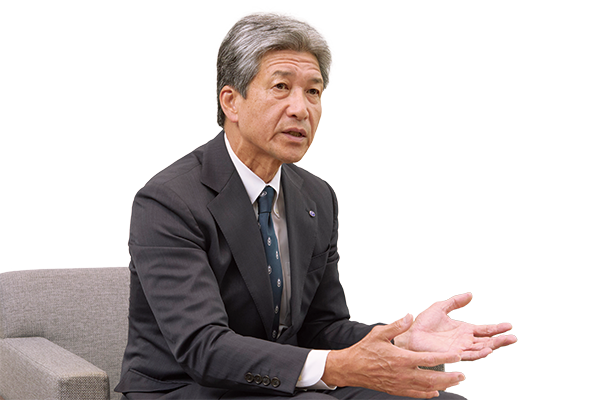
We position the carbon
neutral strategy as a growth
strategy and work on it across
businesses.
Director and Senior Executive Officer
Koshiro Hidaka
We will achieve CO2 reduction with an immediate approach utilizing existing technologies. One of these is to focus on shifting to blended cement production. Blended cement, which has a lower clinker ratio, is in high demand especially in countries with high environmental awareness, and we are positioning the shift to blended cement as an important strategy for our cement business. This is an initiative that contributes to carbon neutrality at the same time as revitalizing the domestic business and deepening our overseas business.
The other is aimed at reducing CO2 through further utilization of waste and by-products, energy saving and higher efficiency of existing facilities, and substitution of fossil energy.
We will also steadily progress demonstration testing of the C2SP Kiln, an innovative CO2 capture technology, and the recovered CO2 fuel conversion process (methanation) technology development, which are being conducted in Sanyo Onoda City, Yamaguchi Prefecture.
Following the 26 Medium-Term Management Plan, we will continue to shift to blended cement, but we will also work on new standardization for its further expansion. As measures in the manufacturing process, in addition to promoting the development and dissemination of gas firing (methane, hydrogen, etc.) technologies, we plan to complete the innovative technologies (CO2 capture and utilization) currently under development by 2030. In particular, with regard to the C2SP Kiln, we aim to realize a carbon neutral plant by completing the technology through demonstration tests using an actual Kiln at DC Co., Ltd., a group company located in Kawasaki City, and combining this with the CO2 capture, refining, transportation, and storage project that we are studying in the project of Japan Organization for Metals and Energy Security . Furthermore, we will complete the technological development of low-CO2 cement, including CARBOFIX cement, and promote its market introduction.
During this period, various innovative technologies, including the aforementioned C2SP Kiln, will be put into practical use and deployed to domestic and overseas plants in order to recover, utilize, and store CO2 that is inevitably emitted during the cement burning process.
In addition, although this is a theme that we will start working on immediately, as well as on medium- to long-term, technological development to respond to disaster reduction and recovery (soil improvement materials, the world's highest strength concrete, etc.), in addition to resource recycling of disaster waste, as measures against severe disasters to adapt to climate change.
In order to realize these, not only will the Group’s technological development and capital expenditure be essential, but we will also need government subsidies, the development of domestic standards, and collaboration with other industries. We will continue to work toward this goal.
●Carbon Neutral Strategy Roadmap
Technological development is steadily progressing, but implementation requires a great deal of investment. For example, we estimate that it will cost more than 100 billion yen to implement the C2SP Kiln at the DC Co., Ltd. plant. If all of this is borne by private companies, the sales price of cement will need to rise to several times the current level. Cost is one of the biggest challenges, and we recognize the need to continue to communicate with customers and other related parties, ask for government support, and raise awareness in society. On the other hand, we can expect costs to decrease as technology advances in the future, and we can also expect changes in the way people think about carbon pricing. We believe that it is important to assess the market value of carbon neural cement and find the right price in order to achieve sustainable carbon neutrality.
●Measures against severe disasters associated with climate change
– Our company's proprietary technologies and future development –
Start of study of a carbon neutral model plant concept utilizing "existing technologies" in the cement production process and new "innovative technologies" that have not been available before.
●Study of the carbon neutral model plant concept
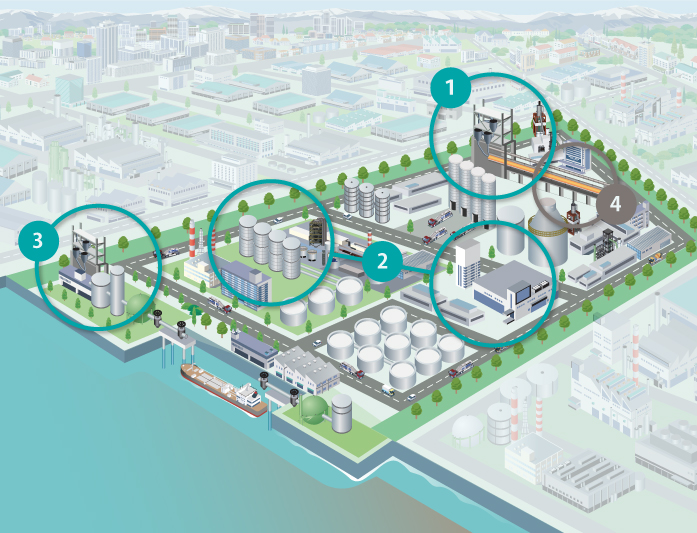
Innovative technology 1CO2 Capture
CO2 that cannot be reduced by existing technologies alone needs to be recovered. In the cement production process, the raw materials are preheated in a device called a preheater, and then burned at a high temperature in a rotary kiln. Most of the CO2 derived from raw materials is generated in a combustion device called a calciner in this preheater. We focused on this point and started the development of a "CO2 capture calciner" that efficiently recovers CO2 from the calciner. By replacing the combustion gas of the calciner from the normally used air to oxygen (O2), it becomes possible to directly recover high-concentration CO2 gas with compact equipment.
Innovative technology 2CO2 Utilization
In order to prevent releasing the captured CO2 back into the atmosphere, effective utilization or storage (CCS) is necessary. As one of the effective utilization measures, we are developing CO2 mineralization (sequestration) technology. Carbonation (sequestration) is a technology that reacts CO2 with calcium in cement-based materials and stably fixes it as calcium carbonate in various concretes. We are also promoting the development of technology for the production of synthetic methane using recovered CO2 as a raw material. Synthetic methane is expected to be used again as an energy source in the cement production process, as well as to be supplied to the existing city gas distribution infrastructure.
Innovative technology 3CO2 Storage
We are also studying CCS for the recovered CO2 as part of the activities of the JOGMEC project consortium. As an overall concept, CO2 recovered from cement kilns is refined and liquefied, transported by ship, and stored at suitable storage sites, and we are promoting efforts toward implementation, such as designing necessary infrastructure facilities and estimating costs.
Existing technology 4Existing Technology
Cement manufacturing requires a large amount of "fossil energy" because it is burned at a high temperature of 1,450°C, and a considerable amount of CO2 is emitted because the main raw material, limestone, undergoes a decarbonation reaction during this burning process. For the former, we are promoting the introduction of energy-saving equipment and the use of alternative fossil fuel. For the latter, we are working on the use of alternative raw materials to replace limestone, the development and diffusion of low-CO2 cement, and the use of supplementary cementitious materials.
●Image of a carbon neutral cement production process
We are currently developing a unique CO2 capture technology called the "CO2 capture type cement production process (C2SP Kiln)," which utilizes technology we have cultivated in cement production. This development is being conducted within the NEDO (New Energy and Industrial Technology Development Organization) Green Innovation (GI) Fund project (~FY2031).
About 60% of the CO2 generated from the cement production process is caused by the thermal decomposition of the main raw material, limestone (CaCO3). In the actual cement production process, the raw materials are heated in a preheating device called a preheater, and then further burned at a high temperature in a rotary kiln. When the raw material passes through a combustion device called a calciner in this preheater, it is heated to a high temperature of about 900°C, generating CO2 (decarbonation: CaCO3→CaO+CO2). We focused on this point and started the development of a "CO2 capture calciner."
In conventional calciners, air is used as combustion gas, but by replacing this with oxygen (O2), it becomes possible to recover high-concentration CO2 gas with compact equipment. Since the equipment can be introduced by replacing the existing calciner, it is not detrimental to the excellent thermal efficiency, that can be said to be a characteristic of the NSP (New Suspension Preheater) which is current mainstream of pre-heating system for cement manufacturing process and waste (raw materials, thermal energy) can continue to be used as much as or more than before.
A demonstration equipment for this technology was completed in March 2024 in Sanyo Onoda City, Yamaguchi Prefecture. The goal of this technology is to realize a global standard facility for the cement industry aiming for carbon neutrality, and we are actively conducting development.
●Gas flow of a C2SP Kiln
By concentrating the calcination reaction of raw limestone in an oxygen-fired calciner, highly concentrated CO2 can be recovered directly from the cement process.
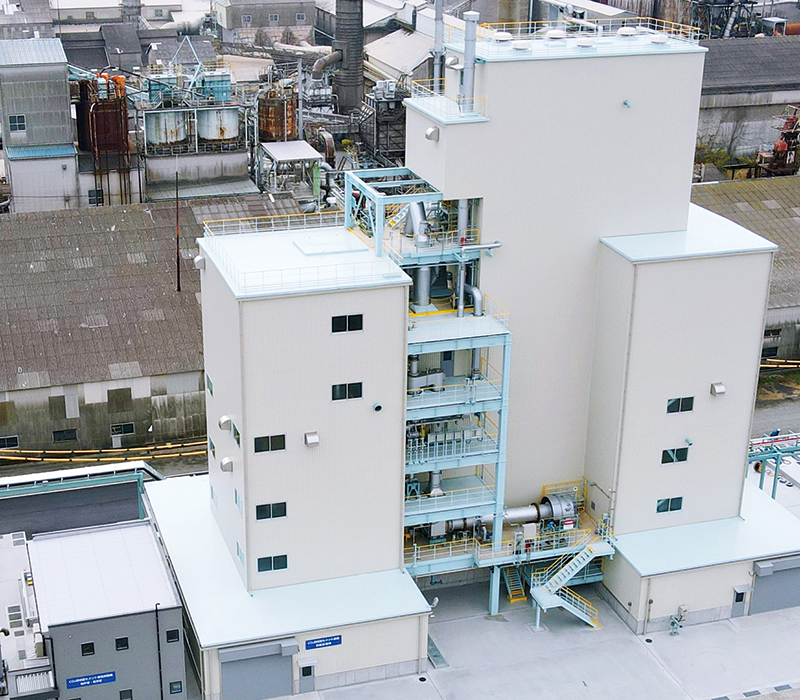
C2SP Kiln demonstration equipment (within the Onoda Plant of Taiheiyo Materials Corporation in Sanyo Onoda City, Yamaguchi Prefecture)
Developer's Voice
Q Please share any memorable impressions that occurred during and up to the completion of the C2SP Kiln demonstration test facility.
A The most difficult thing was that we built such a large facility in a very short period of time. The start of construction was delayed by more than half a year due to difficulties in procuring construction materials, but since the first stage of NEDO's GI Fund project was to be completed by the end of FY2024, we started with all parties involved working together to review the construction process, and we put together all the construction schedules like a puzzle. As a result, we were able to complete the construction in November 2023 as originally planned without any accidents or disasters, and we were able to hold the completion ceremony in March 2024 without any problems. This was of course due to the efforts of all the people involved, but I was overwhelmed with emotion, thinking that it was, in a sense, close to being a miracle. In the second stage from FY2025, we will move to the demonstration test stage using this facility and proceed with the demonstration toward actual implementation.
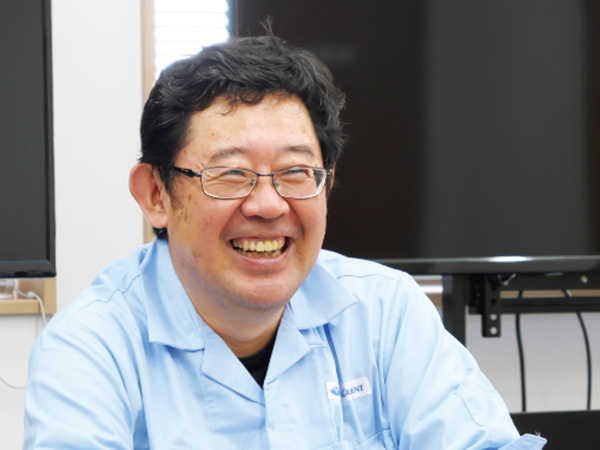
Manager, CO2 Capturing team, Engineering and Technology group, Carbon Neutral Technology Development Department
Kenichi Honma