Towards Value Creation
We are continuously promoting organizational safety, security and health activities with the aim of eradicating occupational accidents, including those in the supply chain, and achieving a safe work environment.
Our Health & Safety Policy is shown below. Under this policy our headquarters and business sites prepare health and safety management policies that suit the actual conditions at the workplace each fiscal year.
We recognize that ensuring the safety, security, and health of our employees is the foundation of our company's existence and, in accordance with the Industrial Safety and Health Act and the Mine Safety Act, we invest appropriate management resources to prevent occupational accidents and work-related illnesses, and effectively implement our Health & Safety Policy.
Based on this, we have established the basic matters concerning safety, security and hygiene management of the Taiheiyo Cement Group in the "Health and Safety Management Regulations," and are striving to promote safety, security and hygiene.
Taiheiyo Cement Health & Safety Policy
We recognize that ensuring the health and safety of our employees is a cornerstone of our company, and we invest appropriate management resources to the prevention of occupational accidents and diseases in accordance with the Industrial Health and Safety Act and the Mine Safety Act, and efficiently implement the fundamental policies shown below.
Health & Safety Policy
- Promote safety, security and health activities through consultation and participation between management and labor, with the aim of eliminating occupational accidents.
- Ensure the health and safety of our employees and those of our contractors by complying with health and safety-related laws and regulations, the health and safety management regulations created by us, and health and safety regulations created by our business sites.
- Strive to improve the level of health and safety by actively promoting the implementation and operation of our Occupational Health and Safety Management System, and by continually ensuring the fundamental safety of our work and equipment, providing education and training, and raising awareness of health and safety, as well as continually improving our Occupational Health and Safety Management System.
- Constantly improve workplace environments and work procedures by applying improved technologies and new health and safety information via the companywide, business site and group affiliate health and safety committees.
- Constantly improve workplace environments and work procedures by applying improved technologies and new health and safety information via the companywide, business site and group affiliate health and safety committees.
Operational Structure
We have established a "Company-wide Health & Safety Committee" under the Sustainability Management Committee, which reports directly to the Board of Directors. The officer in charge of the Maintenance & Engineering Department, which is responsible for safety, serves as the chairperson. The committee oversees the promotion activities of each business site and provides guidance across departments for the safety of group companies, including data collection. In addition, each division at our headquarters, each business site, and each group company has organized "committees and cooperative associations for safety, security, and health" composed of both labor and management, and promotes activities at each business site. Health and safety management at cement plants and quarries in Japan is carried out under our OSHMS*.
* OSHMS (Occupational Safety and Health Management System): Guidelines issued by the Ministry of Health, Labour and Welfare in 1999, a system for continuously and voluntarily conducting safety and health management to reduce potential risks of occupational accidents at workplaces and promote comfortable workplaces.
Roadmap for Realizing the Long-term Vision
The Company-wide Health & Safety Committee conducts a review every quarter in accordance with the aforementioned regulations and OSHMS, and utilizes the PDCA cycle throughout the company. By utilizing the PDCA cycle, we set annual goals that are appropriate for the situation of the entire company.
Among them, we have set unchanging and permanent goals and are focusing on safety, security and health promotion activities.
In FY2024, we set goals and activities based on the review of FY2023 and worked on them.
Target
Zero fatalities across the group (CSR Objectives for 2025)
Materiality Goals/KPIs and Other Goals | FY2022 | FY2023 | FY2024 |
Accident prevention Zero fatalities |
2 | 2 | 1 |
Company-wide Health & Safety Committee Objectives | |||
①Zero fatalities across the group | 2 | 2 | 1 |
②30 or less lost-time injuries across the group | 36 | 49 | 53 |
③80 or less total occupational accidents across the group | 103 | 120 | 133 |
(1) Accidents caused by breaking workplace rules | 24 | 31 | 31 |
(2) Heatstroke-related accidents | 6 | 7 | 11 |
(3) Recurrence of Similar Accidents | 67 | 93 | 97 |
④Absence rate of company employees: 0.5% level | 0.604% | 0.935% | 0.689% |
Implementation of Safety, Security and Health Activities
The results of our activities in FY2024 show that there were 133 occupational accidents, including one fatality, and the absence rate decreased to 0.689% due to the reclassification of COVID-19 to Category 5, but we were unable to achieve our target.
Each business site will gather the opinions of its working employees more than ever before, and all employees will work together with a shared understanding of safety, security and health.
No. of Accidents
Initiatives for ISO 45001
The ISO 45001 standard for OSHMS was established by the International Organization for Standardization in March 2018. Since 2007, our company has been operating an Occupational Safety and Health Management System (OSHMS) based on the guidelines provided by the Ministry of Health, Labour and Welfare. As a global company, in April 2023, our headquarters' Maintenance & Engineering Department (central function), the Kamiiso Plant and the Oita Plant obtained ISO 45001 certification for occupational health and safety, in addition to ISO 9001 for quality and ISO 14001 for the environment.
In March 2024, we underwent a surveillance audit for the continuation of certification at the Oita Plant and re-certification was confirmed without any points to be noted. We will continue to promote continuous improvement using this system.
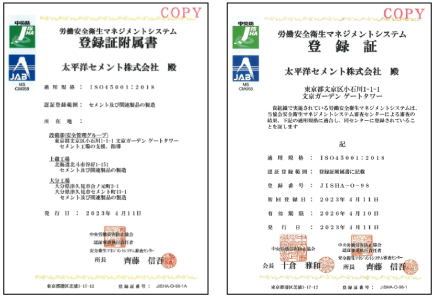
Examples of Accident Prevention Initiatives
Recurrence prevention measures (in response to fatalities)
In August 2023, an accident occurred at a cement plant in which a contractor worker was killed in an accident involving a forklift mast. The direct cause was that the mast was raised and operated while the forklift was in motion, causing it to come into contact with overhead equipment and breaking; however, indirect factors included negligent operation and management of the forklift and lack of visualization of the mast height display. The Company-wide Health & Safety Committee notified all offices of "measures to improve the safety of forklift operations," including the aforementioned measures, and worked to deploy accident countermeasures.
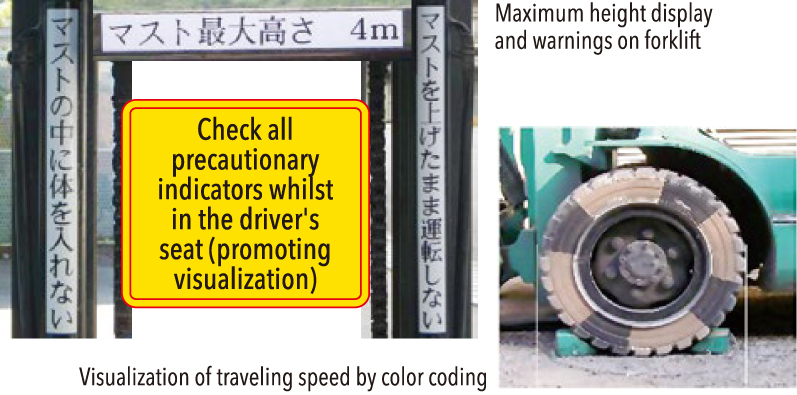
Recurrence prevention measures (activities to pass on lessons learned from accidents)
We are promoting activities to pass on lessons learned from accidents by posting information at accident sites so that accidents are not forgotten. The "visualization" activities raise awareness of rules and encourage mutual attention, leading to improved safety awareness.
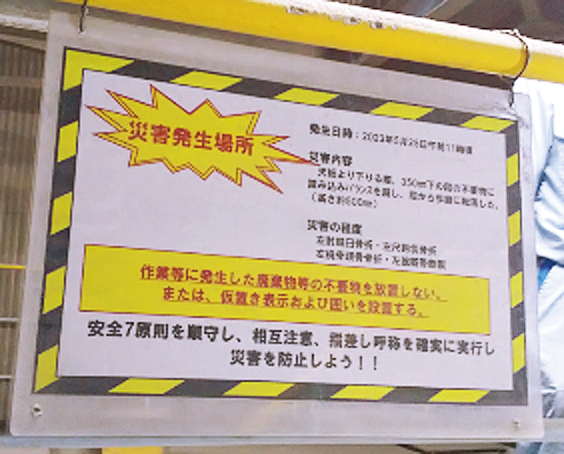
Expanding Safety Activities to Group Companies
The Company-wide Health & Safety Committee supports the safety activities of group companies. We have been conducting safety surveys for the Group's domestic and overseas business sites since FY2019.
FY2022 | FY2023 | FY2024 | |
Domestic business sites | 1 | 7 | 14 |
Overseas business sites | (Activity Restrictions) | 1 | 1 |
Ensuring the fundamental safety of equipment
Each plant is working to ensure the fundamental safety of its equipment by reflecting the opinions from the site.
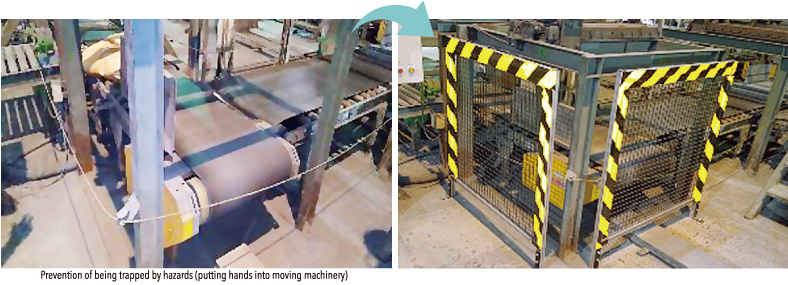
Experiential Safety Training
In order to boost the safety awareness of our employees we hold safety training where they experience risks inherent in familiar operations. Since FY2019, we have been installing experimential safety training equipment at each cement plant and establishing a system that utilizes on-site equipment to provide effective education to young employees and those with little experience. We are also making efforts to improve our sensitivity to safety by incorporating VR education and other innovations.
Introduced hazard experience equipment and tools
Being dragged into (roller, chain, V-belt, belt conveyor, rotary feeder, tabletop drill press, air cylinder) / Safety shoes, falling object impact experience / Hanging with fall prevention equipment (safety belt) / Electric shock and human body electrical resistance experience / Finger pointing and calling safety experience / Heavy object slinging / Disc grinder kickback / Other
Combined with VR education
Falling from heights / Electric shock / Getting caught in a belt conveyor / Contact with heavy machinery